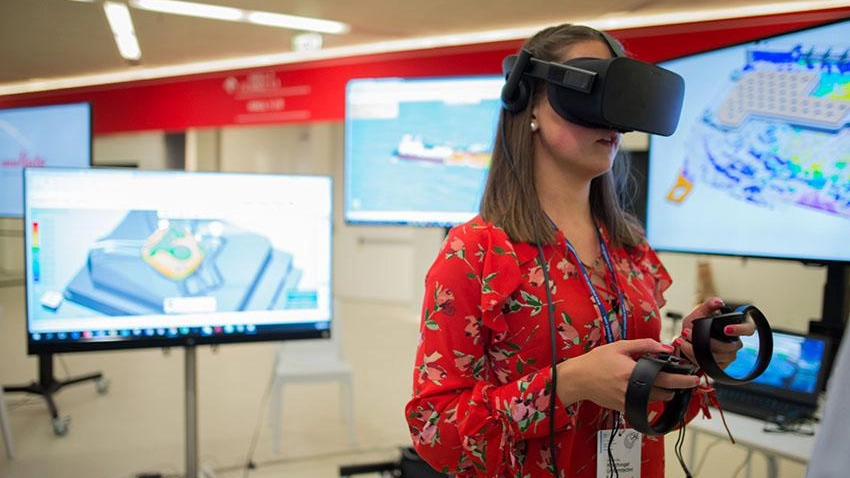
È INUTILE RIPETERSI su quanto sia prioritario per il futuro dell’Italia il Piano Nazionale di Ripresa e Resilienza; esso è un’occasione unica per dare una svolta straordinaria all’intero sistema Paese, nelle molteplici declinazioni del futuro assetto della nostra società. Tale trasformazione passa attraverso numerose componenti innovative, tra le quali assumono rilevanza l’Advanced manufacturing solutions, l’additive manufacturing, l’Industrial internet, la Simulation, la Realtà aumentata, il Cloud e la Cyber security.
Si può senz’altro affermare, anche sulla base della nostra esperienza, che la digitalizzazione dei processi di progettazione, produzione e supporto in fase operativa di apparati e sistemi richiede tecnologie abilitanti quali, ma non solo, la simulazione numerica. Essa è uno strumento indispensabile per sperimentare virtualmente il funzionamento di prodotti o sistemi industriali nelle effettive condizioni reali di esercizio, analizzarne complessivamente le prestazioni e anticiparne modifiche od interventi, abbattendo costi e realizzando test non riproducibili in un laboratorio reale. Formazione e conoscenza, capacità computazionali e tecnologie di calcolo sono aree di investimento necessarie per permettere di trattare un numero sempre più ampio di informazioni legate a problemi sempre più articolati e complessi. La prospettiva di introdurre la simulazione in un sistema allargato, che permetta l’interazione tra il modello di fabbrica e il prodotto in esercizio, potrà divenire soluzione concreta con strumenti interoperabili, standard univoci e modelli predittivi del comportamento di sistemi, macchine e impianti riconosciuti ed affidabili.
Da una recente ricerca (fonte Capgemini Research Institute), risulta che le fabbriche intelligenti potrebbero aggiungere almeno 1,5 trilioni all’economia globale attraverso guadagni di produttività, miglioramenti della qualità e della quota di mercato, insieme ai servizi ai clienti. Ciò sarà possibile se si sarà in grado di affrontare due sfide che stanno emergendo: la capacità di gestire ed integrare sistemi IT con OT, con la dovuta evoluzione ed espansione delle competenze, e capacità necessarie per guidare la trasformazione. La prossima frontiera è l’efficienza dei sistemi di produzione in contrapposizione alla produttività del lavoro: dati sicuri, interazioni in tempo reale e connessioni tra il mondo fisico e virtuale, il gemello digitale, faranno la differenza. Per sbloccare il pieno potenziale della fabbrica intelligente, le organizzazioni devono progettare e attuare una solida agenda di governance e sviluppare una cultura dei processi guidati dai dati, per prendere le decisioni migliori basate su dati disponibili, affidabili e significativi.
Materiali innovativi, soluzioni digitali avanzate e tecnologie abilitanti sono costantemente orientate verso la risoluzione dei problemi del settore manifatturiero, che può tornare ad un adeguato livello di competitività solo incrementando l’efficienza, riducendo il time-to-market, minimizzando i costi e aumentando la qualità di prodotti e servizi. Le innovazioni tecnologiche, che portano a nuovi percorsi di Advanced Manufacturing lungo la supply chain, trovano la loro implementazione quando, raggiunta l’opportuna maturità, riescono ad integrarsi nei processi aziendali con il corrispondente percorso di formazione e riallocazione delle risorse. Oltre agli strumenti HW e SW, tipici di una trasformazione digitale, le persone ricoprono sempre un ruolo centrale per poter gestire i processi, anche con il supporto di strumenti sofisticati, che analizzano una grande mole di dati, affiancati da Intelligenza Artificiale (AI): infatti, solo con strumenti e percorsi decisionali rapidi e affidabili, è possibile estrarre il vero valore dal dato.
L’uso combinato della simulazione (analisi agli elementi finiti, FEA) e dell’analisi dei dati riduce i costi e aumenta l’affidabilità dei modelli predittivi di qualità. Emerge chiaramente che gli investimenti debbano essere orientati alla cultura e alla formazione manageriale e operativa, allo sviluppo della infrastruttura di connettività, alla dotazione di strumenti hardware e software computazionali, individuando target misurabili di avanzamento del processo di digitalizzazione, collegabili all’attribuzione di incentivi temporanei destinati a velocizzare il processo e portare rapidamente il nostro sistema produttivo verso i più elevati standard internazionali.
*Presidente di EnginSoft e direttore tecnico-scientifico dell’International CAE Conference and Exhibition.